Pcb Coil Design Program
Mar 30, 2015 The Coil32 program is coil inductance calculator. All I have said is not in favor of flat PCB coils, however, the compact design along with the use of SMD components often plays a decisive role in use such inductors. You can use the online calculator to calculate the PCB coils on our site. Mar 30, 2015. Precise on-line inductance calculator for PCB inductors with rectangular and round spiral layout.
Start Fritzing and start a new sketch.Go to breadboard view by clicking on the breadboard tab on the top of the window.On the right side is your part-library, select the components you want in your circuit and drag&drop them into the breadboard window. Make sure the parts have the desired specs such as pinout, value and size.
You can change these variables of the selected component in the Inspector to the lower right of your screen.In this example I'm making a circuit that uses an Arduino Nano for switching a 12V relay. For this i need a transistor with a resistor to the base as well as a catch diode in parallel to the relay coil and two screw terminals.The connections/wires between the components are made by clicking and dragging on a leg/pin of the component. Bendpoints in the wires can be made by clicking and dragging inside a wire.Make all the connections you need and would do on a real breadboard for the circuit to work.
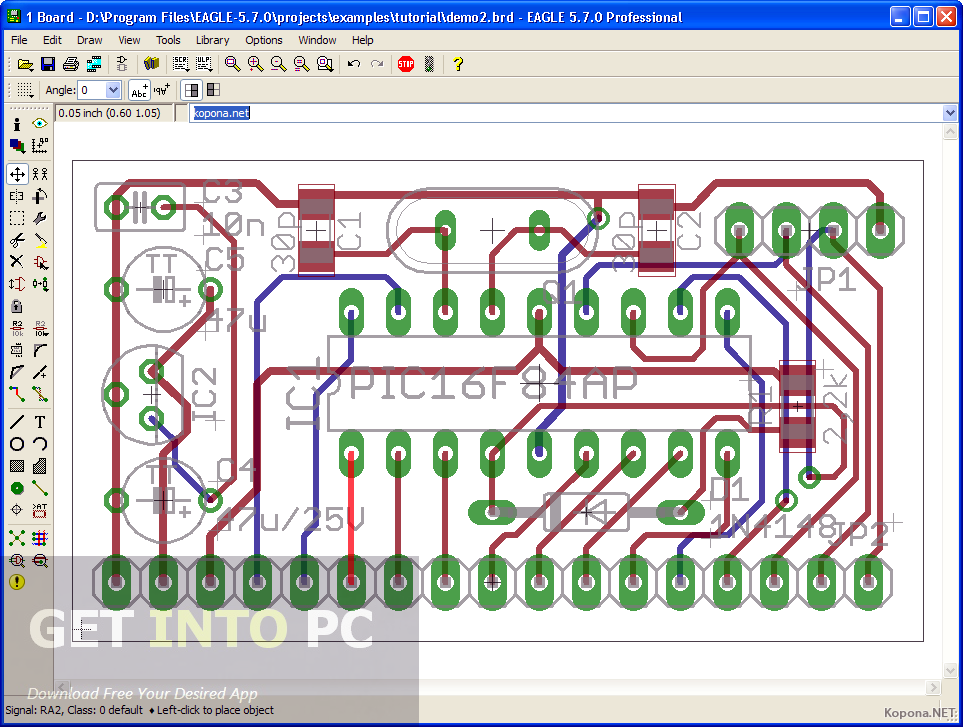
When the Autorouting is complete, tidy up the traces by clicking and dragging their bendpoints. Right click on the bendpoint and select remove bendpoint for removing it.Sometimes there are connections the Autorouter cannot route. You have to route them by hand by clicking and dragging the dashed connection lines. Use Jumpers from the parts library for jumping over traces you otherwise would intersect.You can also add text/logos that will show up in the copper mask by dragging 'Silkscreen Image' or 'Silkscreen Text' from the library to your board.
Select your logo and in the Inspector under Placement - pcb layer dropdown menu select 'copper bottom'. You can load your own.svg files too by clicking on 'load image file' in the inspector. If you think you are ready with the routing click on Routing - Design Rules Check for automatically checking your creation for missed connections / overlapping or intersecting traces.Try to eliminate all errors and repeat the DRC until there are no more problems. Design is finished!Export your PCB as.svg files by clicking on 'Export for PCB' on the bottom. Click on the small arrow on the Export button and select 'Etchable (SVG)'.You will get a bunch of svg's exported in your selected directory but we will only use two of them:.yourfilename.etchcopperbottommirror.svg.yourfilename.etchmaskbottommirror.svgAll other files can be deleted. Select all your traces (but not the inner circles of the pins) and go to CAM - profile operation.If your CNC is GRBL based you may want to do all CAM in makercam in imperial units (see for further reference).
Pcb Design Course
So you have to convert all your millimeters to inches before typing them in.If you're using a 45° V-Bit with 0.2mm tip for the isolation milling process and dive 0.25mm into the material, the effective tool diameter at the surface of your copper clad board is 0.39mm. This converts to 0,015354331 inches, Yayy!As said, we want to go 0.25mm deep in the board, so we're typing -0. Inches as our target depth. The step-down value should be bigger than that so the cutter goes through in one single pass.I found a feed rate of 150mm/min and a plunge rate of 50mm/min to be working well on my machine.Click OK. Reload the page so you're starting a 'new project'.Open the '.yourfilename.etchmaskbottommirror.svg' file. Don't forget to change the SVG-scaling to 90ppi before doing so!Select all holes.Go to CAM - drill operation.I used a 0.8mm drill bit. My board was 1.5mm thick, so for a clean hole i used -2mm for the target depth.
Peck distance should be bigger than this value for the drill to go through in a single pass. I used a plunge rate of about 50mm/min.Click OK and all holes get automatically detected.Go to CAM - calculate all.Export your gcode. Cool, but I have one question.
I am not milling my board with a machine, but rather printing the PCB layout onto a plasic sheet and using it to make boards using the photoresist method. Unfortunautly my dry film is negative, meaning the background needs to be black and the traces need to be left alone. I have looked everywhere on the fritzing program and there doesn't seem to be a way to do this. Is there any way to make the background black and the traces white/transparent by using some other piece of software?
While there are a number of free programs available on the Internet, only a few are actually worth usingin a recent update to the best PCB design software platforms.If you Google “design software for printed circuit boards”, you’ll get close to 2 million hitsThis can be a bit overwhelming for a design engineer, no matter if he / she is in the early stages of a career, or already established within a company.So, how does one go about making sense of all these options? The best bet is to start out with free programs — to figure out what best suits an engineer’s needs first, as opposed to blindly investing in a platform that claims to be the best.There are several things to consider when investigating PCB design software. Among some of the more important criteria:Intuitiveness — The program should have an easy-to-navigate user interface, and be simple to learn. A design engineer should not need to spend hours reading through a manual on how to use the program, nor should time be spent looking for the components library, design tools, et al.Useful features — A lot of programs offer every design feature under the sun, but is this really useful? To be honest, not really. Determine the project’s needs up front and find a program that best services it. A feature-heavy program can lag a bit with too many apps to load each time it’s launched.Well-established — Limit risks associated with unknown / new design software programs, and go with a platform that’s been around and vetted by industry veterans.
New platforms are launched and closed down every day – no project is worth the risk associated with an unknown.Robust library — Large components libraries are extremely important to PCB designers because creating a ton of new components can lead to errors that won’t be captured by the program’s verification tools. The bigger the library, the less chance of error; this, in turn, leads to the program being more reliable for the design engineer.Now, before we get into the five best and free PCB design programs, it is worth noting that this type of platform is a bit limited when compared to its paid-for brethren. It basically allows the engineer to test the service out before moving on to the paid-for versions, with the latter allowing for the more complicated design work necessary for product finalization.So, with that disclaimer out of the way, the following are widely considered the best free PCB design software platforms, listed in alphabetical order:DesignSpark PCB is one of the world’s most popular and easily accessible electronics design software platforms. And for good reason — the program is easy-to-use and learn. It’s constantly updated to improve its intuitiveness in order to better assist the designer in bringing his / her concept to production.
Easily capture schematics, design PCB boards, improve layouts, and more, all with this one program.If you’re just starting out designing printed circuit boards, then ExpressPCB is a good platform to use. It’s a very simple design platform, both in terms of learning how the in’s and out’s of the system, as well as actually using it on a daily basis.
Some features are a bit dated, and the library isn’t that big, so it’s not the best of the best, but it is good enough to use for personal projects, and those just getting started in the field.The two main features that are great about Kicad is that it can be used for any size board (yes, there are programs that limit this), and can be used to create designs with any number of layers. But, with this being a free program, there are some pitfalls—chief among them, the user interface (a bit dated) and the library (a bit limited). Regardless, at the end of the day, Kicad does get the job done, rather reliably, and for that it deserves this place on the list.For the slightly more professional-minded design engineer, PCBWeb Designer is about as solid a free program as they come. It’s easy to install, use, and learn.
The components library is fairly robust, and the user interface intuitive. Also worth noting – the program includes an integrated Digi-Key parts catalog with bill of materials manager, to make purchasing the necessary components seamless.If you’re looking for a simple program to design schematics, you can do no wrong by going with TinyCAD.
It doesn’t come with the features of a paid-for program, but there is genius behind its simplicity—it’s a very responsive program that is also extremely intuitive. The library isn’t that large, but creating new components is pretty straightforward. Also, if you’re looking to print / share your designs, you can publish them by copying and pasting them into a Microsoft Word document, and then saving it as a Word File,.PNG, or.PDF. 8:15:42 AMYou may be surprised to learn this Web-based EDA suite -Runs in browser. Schematic capture, Ngspice based simulation, PCB layout.
Tool is free for users. All files in open format JSON. Can import Altium, Eagle schematics and also LTspice schematics for (limited) simulation and for conversion to PCB with full BoM support. Spice netlist import and export.
Altium, PADS and Free PCB netlist export. PDF, PNG and SVG image export of all files.Users can download Gerbers and are not tied to the tool for PCB manufacture but they can buy PCBs and fully assembled PCBAs from EasyEDA if they wish. 7/12/2016 3:23:16 PMAs an update to the comment above.' From our sister site, 3D Fixtures™, you can easily get mechanical parts for your circuit board projectBeyond solid pieces, our service is also capable of producing fully-functional moving parts (i.e. Bearings, pulleys, and cranks). Click here to read our latest blog post on these 3D printed moving parts. At Sunstone Circuits®, we know that your prototype is made from more than just circuit boards.
To bring your vision into reality, you might need custom brackets, clips, connectors, or even high-quality enclosures. That’s why we have 3D Fixtures™. Our passion for the electronics entrepreneur enables us to provide these solutions, quickly and at an affordable price.To illustrate how this can work in real life, we built a smart watch utilizing Sunstone's design tool (PCB123®), our manufacturing facility for the boards, our assembly partner (Screaming Circuits) for parts insertion, and 3D Fixtures for the watch case/bracelet. In addition, 3D Fixtures quickly made more » a test/programming jig to facilitate that piece of the process. Details can be found here.Please visit our site for general information and to register for updates at www.3dfixtures.comor call 1-503-980-4362.Who is 3D Fixtures?3D Fixtures applies Sunstone's philosophy and values to 3D printing and additive manufacturing, in order to deliver precision acrylic 3D parts used for enclosures, manufacturing jigs, fixtures, and short-run production parts.
We pride ourselves on providing high quality, quick turnaround, often in less than 24 hours and affordable pricing. We closely review every design for manufacturability and work with our customers to save both time and materials. Our state-of-the art industrial machine with materials, resolution, tolerances and finish quality coupled with an experienced technical staff will provide you a solution for the parts you need.Connect with Sunstone Circuits online!Visit our site at www.sunstone.comMailing address:«less.